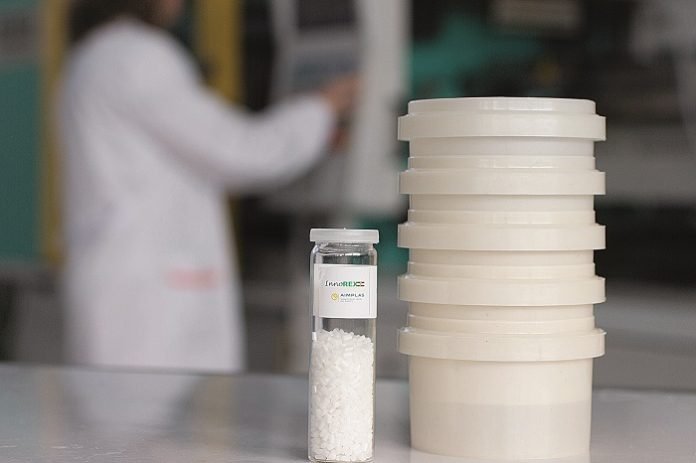
Aimplas, the Plastics Technology Centre, has completed its participation in the European project Innorex By means of these researches, it has been possible to develop an innovative process to obtain polylactic acid (PLA) improving its mechanical properties
and thereby allowing its application in injected packages and replacing polypropylene.
The primary innovation in the process of PLA achievement developed within the project is the use of an extruder as a reactor to produce PLA from lactide. This technology allows doing away with metallic catalysts and using alternative energies to improve the reaction’s kinetics, as well as doing a measurement in line with material viscosity during the process. A wide research has been carried out, related to how the final properties of biopolymers are modified by adding additives or fillers, where a modified PLA has been achieved with more flexibility and 200% more resistance to impact than the conventional one.
Due to these improvements in its properties, it has been established that the new material can be used in food packaging manufacturing by injection and thermoforming, where PLA can replace polypropylene. In this way, the company is contributing to reduce the consumption of conventional plastics by others. Moreover, the elimination of metallic particles in the process will result in a marked improvement in the environment, offer better safety standards for workers, as well as provide an opportunity for the application of these biopolymers in new sectors, such as biomedicine.
After an intensive research, the synthesis of a new eco-friendly and organic catalyst to catalyze the polymerization of lactide has been achieved, thus getting a robust conversion of monomers to obtain a high molecular weight PLA with good polydispersity and optimal optical purity. In addition, the results obtained are reproducible at bulk scale and there is the possibility of extrusion.
The procurement of PLA has been made by means of polymerization by Ring-Opening Polymerization (ROP) through a reactive extrusion process that unifies in a unique process the chemical and pellet synthesis. Moreover, the use of alternative energies, such as microwaves or ultrasounds, has allowed energetic reduction up to 20% when obtaining the final material.