
In some ways, this year’s European Label Expo has been a difficult show to report from because I had expected to see lots of new machines after the pandemic-enforced four-year break but in reality, most vendors had already announced their machines previously so that the main interest was around emerging trends rather than individual news items.
All the talk on the first day was about the unbearable heat in the halls and the lack of air conditioning. Some vendors complained that visitors were too hot to stop and just kept moving from one stand to the next. To start with, many people that I spoke to were hesitant about the planned move to Barcelona for the show’s next outing in 2025. But by the end of the first day, most people were looking forward to the modern facilities and air conditioning that Barcelona’s Fira ground promises.
It does seem to me that the role of digital label presses is starting to evolve more fully. In the past, many converters bought digital presses to supplement their flexo production by taking on shorter-run jobs. The pandemic forced many converters to reevaluate their approach to digital, which also allowed them to pivot quickly to take on different markets – typically food and health products – to match rapid shifts in consumer demand.
This raises the question, which is most efficient – a roll-to-roll digital press with offline finishing; or a hybrid machine that can do everything in a single pass? Bui Burke, senior vice president of sales for Screen Europe, estimated that about 80% of customers preferred a standalone digital printer. However, Jed Hardcastle, business development director for Dantex, said, “In Europe, people mainly look for hybrid but in the USA they go for more roll-to-roll.”
Bobst – Digital Expert 340
Bobst took an interesting approach to this question. Bobst was the only one of the major inkjet press manufacturers to announce a new inkjet press at the show with the new Digital Expert 340, which is a roll-to-roll inkjet press. And yet, rather than show off this new press, Bobst chose instead to showcase its existing hybrid model, the Digital Master 340. I’ve already covered Bobst’s presses in a separate story but it’s worth noting that although the Digital Expert and Digital Master use the same inkjet print unit, the main difference between the two is the speed.
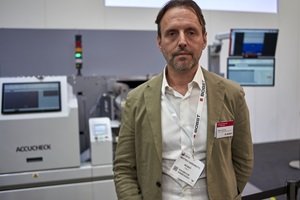
Photo Nessan Cleary
The Digital Master hybrid runs at 100 meters per minute while the Digital Expert is limited to 65 meters per minute, though this can be upgraded to 100 meters per minute through a license to unlock the software. Matteo Cardinotti, who heads up Bobst’s narrow and mid-web division, explained, “The entry-level speed is limited to lower the investment cost of the machine. The market is big worldwide so for some companies, 65 meters per minute will be enough to replace a technology that is slower.”
He added that on the hybrid machine, 100 meters per minute is fast enough to be a viable alternative for a flexo press for the labels and packaging markets. He says that the choice between flexo and hybrid depends on the market and application but notes, “I would say that the hybrid is more popular now. It’s newer.”
It’s also worth noting that the Digital Expert is a 340 mm press whereas the Digital Master is available in both 340 mm and 510 mm widths.
Gallus One inkjet press
Gallus showed off the Gallus One inkjet press that it had announced last year which I’ve covered in more detail here. As I noted in that story, this feels like a work in progress to me. So far Gallus has modernized the underlying chassis by switching to the modular Labelmaster as the base. This means that the Gallus One is compatible with the full range of flexo units that were designed for the Labelmaster. It also opens the possibility that Gallus can develop wider versions of the inkjet press since it already has 440 mm and 570 mm Labelmaster chassis available to it.
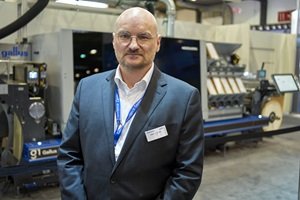
Photo Nessan Cleary
However, Gallus is still working on the digital print unit. This means that at the moment it’s a five-color press – CMYK plus white – running at a maximum speed of 70 meters per minute, though there is room to add three more ink channels. For now, the Gallus One is the slowest of the major presses that are using Fujifilm Dimatix’s Samba printhead. The Samba has emerged as the gold standard in the narrow web market, with both Bobst and Durst managing to run at 100 meters per minute at 1200 dpi with this head. That in turn suggests that Gallus ought also to be able to hit that sort of speed. Dario Urbinati, CEO of Gallus, told me, “At the end of the day what we need to achieve higher speed is an additional round of development with higher viscosity ink. We are not there yet when we can publish anything but we do have the ink formulation.”
Durst – new announcements
This brings us to Durst, which had a couple of interesting announcements, though little in the way of new equipment. Firstly, Durst has committed to expanding its arrangement with Omet over the jointly developed XJet hybrid press. Essentially this is a Durst RSC Tau digital press with Omet flexo units on either side. Durst will now take on the sales and marketing for both the digital and conventional parts of this design and bring it fully into the Durst portfolio. This should also give Durst more freedom to further develop this integrated concept. That said, the XJet itself, complete with a Durst Tau RSC 510 mm wide inkjet press, was shown on the Omet stand.
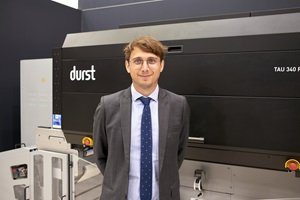
Photo Nessan Cleary
Durst did introduce a new quality control system that it calls Hawkeye. This is based on a single scanner that covers the whole print width. It is able to pick up missing colors but does not include a spectrophotometer to measure any spectral data. For now, it runs at 80 meters per minute though some of the Durst Tau presses can run at up to 100 meters per minute. Product manager Martin Leitner says, “The next development will be for 100 meters per minute.”
The Hawkeye can be retrofitted to all of Durst’s RSC series label presses, meaning those with Samba heads, He says that the nozzle compensation is part of the Dimatix Samba printhead system, which allows for blocked nozzles to be switched off and for adjacent nozzles to print larger drops. But he adds that the Hawkeye system builds on this by locating and compensating for the blocked nozzles in real-time at speeds of up to 80 meters per minute. He explains, “Most systems work in set-up mode or in maintenance so the operator needs to print a special test pattern and this needs to be cut out in the post process.” He says that most alternative systems just perform comparisons with a master image, adding, “But the Hawkeye is not doing that. It uses an AI algorithm which we trained with millions of samples of good and bad labels. This was a huge amount of time and makes the press easier to use.”
There is no setup needed so the operator doesn’t need to teach it or to set the sensitivity. It works fully automatically in the background with continuous inspection and correction of the print. Leitner continues, “When it logs a mistake the operator can check it to see if it’s really a mistake or good enough.”
Durst developed the Hawkeye system with CoVision Lab, a software company that Durst co-founded and which specializes in deep learning and AI technology. Leitner adds, “They have other products like 3D modeling and that’s also where Durst is going to have the possibility to have this resource in-house which can talk to our software engineers from prepress to print.”
Leitner says, “We are lifting inkjet to the next level. We are starting now to understand the prints because we are able to get real data about the behavior of the nozzles and the printheads and we can use this data to drive specific actions.”
The Hawkeye will fit into Durst’s analytics service package. It should show if a specific printer is performing worse than expected and if the service regime needs to be changed for that press. Leitner adds, “It will allow us to have much more possibilities where we have people managing a fleet of machines. The system has a price but we feel that the ROI will be quite quick.”
Naturally, Durst is also considering which other parts of its portfolio can benefit as Leitner notes, “We have the core technology. We start with the single-pass label machines. It doesn’t make much sense on multi-pass but I think it’s a logical step for other single-pass machines.”
Screen – hybrid line
Screen showed a hybrid line that combined a Nilpeter FA with its Truepress L350 UV SAI inkjet label press. Screen has long had a hybrid option with Nilpeter but this has now evolved into a more integrated approach. Burke explains, “We have the Nilpeter people all the data they need to join with our press so customers can choose whatever units they want.” He says that even though the majority of presses are sold as standalone units for greater flexibility, there’s a lot of interest in this hybrid approach. Burke adds that Screen has become open to partnering with other vendors and that all the codes and connections are fairly standard so Screen should also be able to integrate with other manufacturers.
Screen also showed a prototype of an inkjet primer unit within the L350 SAI press that’s designed to improve ink adhesion on the more difficult substrates. This has meant adding an extra print bar with pinning immediately afterward before the other colors. That in turn means that it can’t be offered as an upgrade to existing customers. It should be commercially available early next year.
Otherwise, the SAI press itself can take up to seven colors – CMYK plus white, blue, and orange. It runs at up to 60 meters per minute at 600 x 600 dpi resolution though this speed slows down to 50 meters per minute.
Screen also showed the same prototype of its Pac520 single-pass inkjet as was previously seen at the Hunkeler Innovation Days and Interpack earlier this year. Screen has adapted the existing TPJ520NX to create a new press for printing to paper-based packaging. However, Screen is still testing the materials and tweaking the ink formulation so this is unlikely to be commercially available until early next year.
Domino – inkjet module
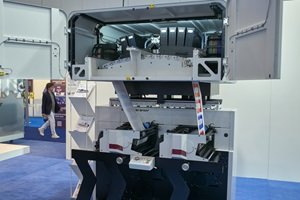
Photo Nessan Cleary
Domino used the show to announce a new inkjet module that can be retrofitted to flexo presses to create a hybrid press. The N610i-R unit is based on the existing N610 platform and uses the same Kyocera printheads. The base model uses four colors – CMYK – and there’s a 5-color version with two printbars for white ink. Domino has gained a reputation for producing highly opaque white ink, claiming up to 72% opacity. There’s a choice of ink sets, including the standard UV90 and UV95, which are suitable for non-direct contact food packaging.
It was shown with flexo units from Mark Andy but Paul Bunyan, workflow solutions consultant for Domino, says that it’s relatively straightforward to adapt it for use with other manufacturers if customers require it. It has a 330 mm print width. Resolution is up to 600 x 600 dpi at 50 meters per minute. Bunyan says it is possible to increase the speed by changing the waveform to produce three drops instead of four.
In the next part of this story [to appear in Packaging South Asia‘s December issue] I’ll look at some of the other inkjet presses, with the toner devices to come in a further part.
First published on 11 October 2023 in the Print and Graphics Journal www.nessancleary.co.uk
Published by permission.