Paul Callaghan, the organizer of the two day Shift_019 packaging conference in Delhi’s Aerocity, was forthright. He encouraged the participants to pay attention to their own benefit, right from the start on the first day of the conference. He rightly assumed that the audience was there to learn and absorb the technical information that can help them make business decisions. The sponsors and speakers comprised a very strong contingent of technology and equipment suppliers and some of the best packaging and label converters in Asia.
The highlights of the first day included presentations from Flint and Miraclon (formerly Kodak’s flexo business) that spoke about the advances in flexo platemaking. Taken together, the two presentations by Supachai Theravithyangkura, technical director of Flint Asia Pacific, and Hrishikesh Kulkarni, manager – Flexible Packaging Division at Miraclon, reinforced the increasingly apparent improvements, namely that flexo prepress technology is increasingly competitive with gravure quality – both in terms of fine detail and color consistency. It is also moving forward to become a robust industrial process. Robust for flexo means consistency and predictability with stable platemaking processes, where a variety of desired results can be designed and achieved by the choice of workflow, technology, equipment and materials. These are now available and much easier to use.
On the morning of the second day, DuPont added more take-home value for us in the improvement of flexo discussion. Gururaj Kirsur, territory manager of DuPont Advanced Printing in South Asia, talked about improvements both in the return on investment and in sustainability. For example, he talked about newer ways of printing solid whites on flexible materials that actually decrease the ink consumption while maintaining the same quality. His approach holds flexo up to a high standard both as far as quality and costs. Kirsur put the focus on processing flexo plates without VOC-based solvents and the beneficial safety and health implications of the process. He also equated faster digitally imaged flexo platemaking using thermal processing with just in time plates, safety and health that ultimately led to better ROI.

The presentations by Bobst, Uteco and W&H on Day 1 also centered round the technical advancements in flexo printing although all three companies are equally adept at both gravure and flexo. They each presented developments in automation and new methods of color quality control that are driving the reliability of flexo and enabling it to continue to encroach on gravure’s territories even in Asia. Without taking sides in this flexo versus gravure discussion, which is not really a debate (since each has its appropriate and necessary use at this point), one must add that there were a number of leading converters in the audience who have produced excellent reverse printing on CI flexo presses as well.
Alfred Ulli of Bobst described a very interesting and advanced process that was recently shown in Italy that it calls digital flexo and uses digital dosing and inline measurement to achieve precise color on narrow web flexo presses currently.

Anuj Sahni of W&H spoke about both extended color gamut for which his companies are ready today and the need for improvement in color management since, “50% of press downtime today is because of color matching and management. In our new system, live color management is uploaded to the Cloud and the customer can see the quality as it is being produced.” Sahni also added that no longer can merely generic machines be produced – “Every machine has to be customized for not only the converter but with the focus on the brand and the consumer.”
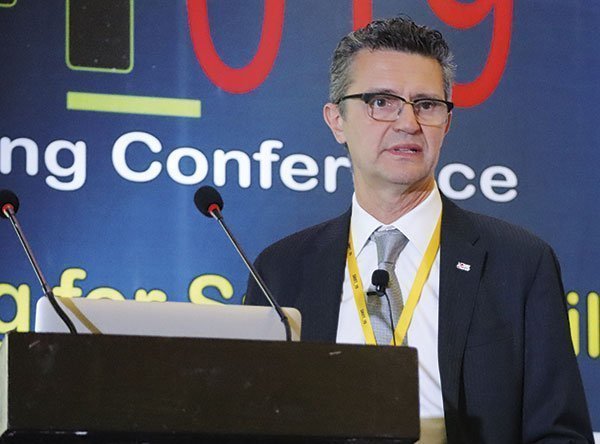
Giuseppe Sauli of Uteco added to the sustainability and automation themes being discussed by several speakers. Increasingly the company’s CI flexo presses are used with water-based inks although there are several issues and in many cases it is the customers that are not ready for change. Showing global packaging trends he asserted that CI flexo, especially with some of the new automation systems such as automatic setup software, control optimization for each color unit and software for checking the contact position between the plate, anilox and CI drum, is the way forward. Pressure setting for startup is being automated and register controls are coming to each deck in conjunction with color matching systems that are able to easily reach a Delta E of +- 2.
David Jones of Alphasonics spoke about both the wastage of materials and damage to the environment of putting UV and solvent-based inks into drainage systems. Speaking about his company’s Betasound anilox cleaning system developed for effective cleaning across a wider screen count range and especially for HD flexo, he said, “This is the first multiple frequency, variable power, super sweeping ultrasonic cleaning system. It uses higher frequencies that are more gentle, is future proof and ultra-safe.” Using active cavitation, the new system saves a great deal of time for cleaning anilox rollers.

Klaus Nielsen of Xeikon Asia Pacific based in Singapore spoke about the possibilities of being both green and profitable in packaging using digital presses. He presented four possible strategies for avoiding the hypercompetition in the packaging market using digital presses that are inherently green since they require little makeready waste and produce only the required number of sheets. These strategies include the short run approach; that of being the most cost-effective; the most innovative; and, perhaps being a disrupter. Nielsen made clear that investment cannot be a ‘me too’ event; it requires serious market analysis and a creative approach to take advantage of new technologies that offer many possibilities but cannot be profitably executed without solving a felt need in the market or perhaps even by inventing a need that has not been traditionally recognized.
There was also a WOW presentation by Lindsay Nutley of Australian label converter QLM. Nutley, who is based in the QLM plant in Vietnam, spoke about the new culture of communication and marketing one’s services by actually using these to implement both customer and employee engagement. Nutley made clear that it’s the company’s leadership that needs to create the message and a branding eco-system and then to use the marketing people and the entire company to communicate this message.
The speakers and sponsors comprised a veritable list of some of the best suppliers to the packaging industry. A partial list included Alphasonics, ALPS, Baldwin Vision, Bobst, CGS, DIC, DuPont, Flint, HP, IPAMA, Kornit, Koenig-Bauer, MPS, Martin Automatic, Memjet, Milacron-Kodak, Monotech, Uteco, W&H and Xeikon. As far as quality information, the conference was good, the panel discussion awakened the audience and the awards dinner on the second day brought in a bit of glamor and converter participation from the region to the event. The next Shift_20 conference will take place in Vietnam.