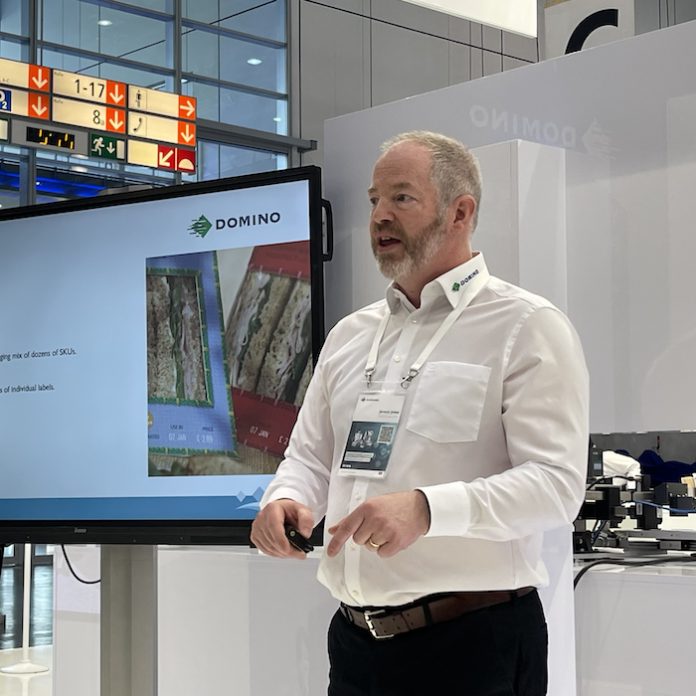
Domino at interpack talked about optimizing investment and improving manufacturing efficiency and output by prioritizing investments on the ‘journey to zero.’ The company’s ideas and proposition presented at the show along with its latest technology included a subscription-based business model for smart manufacturing solutions and integrated coding and marking technologies. The company offers flexible finance options to allow manufacturers to access the latest technological advancements without capital investment.

Photo PSA
The solutions shown at its stand included Domino’s advanced coding automation software; its cloud-based solutions for remote performance monitoring; and, external vision systems for simplified code inspection. The company talked about helping manufacturers to target ‘zero’ waste on their production lines.in coding and marking technology using its ‘Waste Calculator’ for helping businesses quantify costs and prioritize investment on their ‘Journey to Zero.’ Apart from showing its wide array of coding and marking engines Domino talked about its ‘no investment” services’ – a subscription model for its technology implementations that include maintenance and continuous data loops using the cloud.

At the Domino press conference at its stand, Amaia Cowan of Futamura presented a use case for the Domino waste reduction solution for the production and packaging of its NatureFlex cellulose film using Eucalyptus wood pulp from sustainable forests. The compostable packaging solution is seen as a good fit for the circular economy. Another sustainable solution highlighted at the press conference was Sappi’s evolving barrier recyclable solutions for its packaging papers. As we have written earlier, Domino provides its laser based coding solutions for transparent fresh food NatureFlex compostable film packaging.
Domino’s Waste Calculator is designed to highlight key areas where production line inefficiencies and errors can lead to excess physical and financial waste. Jeremy Jones, Global Marketing director of the company in his enthusiastic presentation at the press conference said, “As manufacturers, we are all looking to improve manufacturing efficiency and output. Reducing unnecessary costs and waste is a crucial part of this. Domino’s Waste Calculator helps identify where inefficient processes and errors could be contributing to wasted products and, by extension, wasted energy.”
“We outline the steps manufacturers can take to ensure that the energy, time, and funds they invest are spent creating the maximum possible number of high-quality, sellable products for profitable, sustainable manufacturing – rather than waste.” Domino’s Waste Calculator provides users with a bespoke in-depth report or a simplified, industry-average-based overview of five hidden causes of production waste – manual data entry; manual code inspection; unreliable technology; service delays; and, lack of integrated data.
“It is almost impossible to develop long-term sustainable solutions without understanding the causes and costs of manufacturing waste,” continued Jones. “Our data suggests that, for an average manufacturer, waste from manual label creation could amount to over US$ 100,000 annually, while waste from service delays resulting in the loss of a single shift could cost well over US$ 50,000 per outage. We are here to share this data and help manufacturers to make the right choice.”
Jones concluded, “Domino’s closed-loop solutions are designed to tackle each of the hidden causes of waste by minimizing the need for manual intervention and ensuring accurate transfer of product data; providing clean, reliable, and verified code placement; and limiting unplanned downtime either due to inefficient product changeovers, or machine failure.”