With its manufacturing base in Dadra and Nagar Haveli, about 200 km from Mumbai, Saptagiri Packaging is aggressively chasing growth and has invested in state-of-the-art equipment for its printing as well as converting divisions. It has also expanded its plant and invested a significant amount of capital on modernizing it. On 24 September, the company formally inaugurated its expanded plant that now has an area of 100,000 square foot spread over three floors, doubling the area it earlier had. It also formally commissioned a brand-new Heidelberg CD 102 6-color press with UV coater and a brand-new Bobst Novacut 106 diecutter. The company specializes in blister back-up cards and supplies to customers in the FMCG and agro-chemical industries.
“Every company aims for growth because with growth comes profit. The only way we can achieve growth is by constantly investing in technology,” says Nikhil Warrior, executive director of Saptagiri Packaging.
Saptagiri is already familiar with both Bobst and Heidelberg technologies as it was using a second-hand Bobst 102 SE diecutter, a Bobst folder gluer and a used Heidelberg Speedmaster CD 102. However, Warrior says this time the company decided to opt for only brand new machines, given the less than satisfactory experience it got in bringing the used machines to production level.
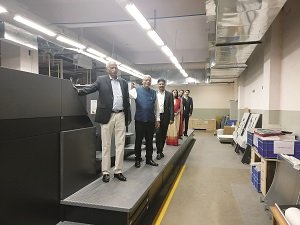
“We are really happy with the combination of Heidelberg in the press section and Bobst in the converting department. So, we wanted to continue with that combination when we were planning to buy the new machines. In case of Novacut, the main advantage was the feature of double cam sector drive mechanism, which ensures lifetime registration accuracy of +0.01 mm to -0.01 mm. That is what sets them apart from the rest. As for Heidelberg, there is not much to be said as we have reached where we are now using their printing technology and we have great trust on that brand,” he shares.
The Novacut 106 can handle maximum sheet size of 1,060 mm x 740 mm and minimum sheet size of 400 mm x 350 mm. Its specification when it comes to stock thickness range is as follows: paper minimum 80 gsm, carton or solid board up to 2000 gsm or corrugated board up to 4 mm. The Novacut runs at a maximum speed of 8,000 sheets per hour.
The Speedmaster CD 102 is the right choice for packaging print shops in India. It processes board up to 1 mm thickness with ease. Plate changing with AutoPlate is also quick and easy. The contact-free sheet transport with the AirTransfer system and the high storage capacity of the inking system deliver high-quality print result. The UV coating unit of the Speedmaster CD 102 is fitted with a chambered blade system to meet the most exacting coating requirements and rigorous finishing standards. Saptagiri’s CD 102 is a 2017 edition from Heidelberg and equipped with sturdy grippers and bearings of the XL 106 press and deliver high print quality with a speed of 15,000 sheets per hour on varied substrates.
After the commissioning of the new Heidelberg and the new Bobst, Saptagiri now has three Heidelberg presses in its printing section, two Bobst diecutters, one Bobst folder gluer and H+S liner machine in its converting division.
Greater push into the folding carton segment
With the new Bobst and Heidelberg on the shop floor, Saptagiri Packaging now has a capacity to convert about 1,000 tons of paper board every month. Having established itself in the blister cards segment and with more than double the manufacturing area than before, the company is now looking to give a major push into the folding cartons segment. An E-flute line is expected to come up soon and Warrior is looking to buy a corrugation machine with its finishing machine. “We have not decided on the brand of corrugation and finishing machine. We are considering a few options and Bobst is for surely one of them,” he shares. Saptagiri is now looking at producing mono cartons, litho laminated carton, metallized cartons, etc.