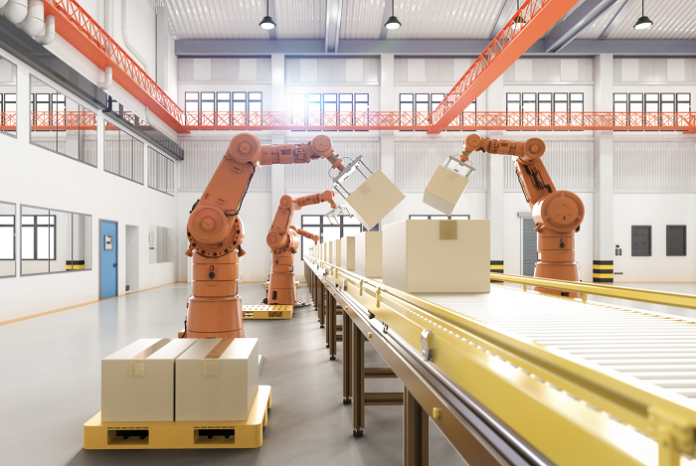
In packaging, traditional inspection involves manual checking, which is time-consuming and prone to human error. In contrast, AI-powered packaging inspection systems use advanced technologies, instantly identifying defects and recording data in near real-time. This process ensures consistent and accurate inspections, significantly reducing the time required from hours to minutes, thereby increasing productivity and reliability in identifying packaging defects.
AI-powered packaging defect detection is triggering a change in the industry by enhancing efficiency, accuracy, and consistency. These systems can quickly scan and identify defects with high precision, significantly reducing the inspection time from hours to minutes, says Sunil Kardam, consulting and analytics lead at Gramener, a design-led data analytics & engineering company. It not only enhances productivity but ensures higher quality standards, minimizing the risk of defective products reaching consumers.

“The automation of defect detection reduces human error and labor costs, making the packaging process more streamlined and cost-effective. This solution is particularly crucial for industries dealing with packaging of expensive items such as alcohol, jewelry, and electronics, where quality is paramount,” he added.
At present, there is no widely available solution customized to detect defects in packages in India, Kardam told Packaging South Asia. Previously, the solutions were very expensive and there was a lack of client readiness, he said, adding the scenario is now changing as more cost-effective solutions can be developed with the advent of large language models. The packaging industry in India is growing rapidly, with a significant market size and a high CAGR growth, indicating a strong potential for adopting AI-powered solutions, he explained.
Impact on quality & brand reputation
AI significantly enhances packaging quality by ensuring consistent and precise defect detection, which reduces the likelihood of defective products reaching the market. This consistency in quality control strengthens brand reputation as consumers receive high-quality, defect-free products. By minimizing human error and improving inspection accuracy, AI helps maintain high standards, fostering trust and reliability in the brand, and potentially leading to increased customer loyalty and market share, Kardam said. Compliance with industry standards further enhances quality and reputation.
AI packaging detection methodologies drive production efficiency
AI-powered packaging detection methodologies improve production efficiency by drastically reducing inspection times from hours to minutes. Automated systems can perform real-time defect detection, allowing for immediate corrective actions, Kardam said, adding this reduces downtime and enhances the overall production flow. The consistency and accuracy of AI inspections eliminate rework and reduce waste, leading to a more streamlined and efficient production process, ultimately increasing throughput and reducing costs, he said.
AI-powered packaging inspection methods can identify a wide range of defects, including surface defects such as tears, dents, stains, wrinkles, creases, color smudges, and any damage to logos. They can measure the size of defects and identify shade or color variations. These systems use advanced computer vision models to detect even subtle imperfections that might be missed by human inspectors, ensuring that only high-quality packages reach the customer, and enhancing overall product integrity and customer satisfaction.
“Machine learning is incorporated into manufacturing processes by training algorithms on large datasets of known defects. These algorithms learn to recognize patterns and anomalies that indicate potential defects. This allows for the early detection of issues that may not yet be visible to the naked eye. Images from cameras are analyzed continuously, enabling timely intervention, which helps prevent defects from progressing and ensures higher quality standards. Gramener’s use of GenAI and vision LLM models enhances this capability by providing faster implementation, good accuracy, and the generation of synthetic data to improve defect detection,” he said.
AI & packaging automation
AI helps with packaging automation by integrating advanced image recognition and machine learning algorithms to automate the inspection process, Kardam said, adding that these systems enable real-time defect detection and data recording, streamlining the inspection workflow.

Automated alerts and report generation reduce the need for manual intervention, allowing for continuous and efficient operations. This automation leads to faster, more accurate inspections, reducing labor costs and enhancing production efficiency, he said. The applicability extends to primary, secondary, and tertiary packaging, covering all stages of the packaging process.
Gramener provides AI-powered packaging detection methodologies that leverage advanced image recognition and machine learning, including GenAI and vision LLMs models. These methodologies include real-time defect detection, automated data recording, and customized report generation.
“Gramener’s solutions are designed to be flexible and mobile, allowing inspections to be performed anywhere, including on production lines. They incorporate industry standards like TAPPI and ASTM, and enable the identification of customer-specific defects, ensuring that packaging plants can maintain high-quality control and efficiency. Users can analyze defect trends, update the defect list, and generate synthetic data to augment the inspection process, ensuring continuous improvement and adaptability,” Kardam said.
Sustainability and reducing waste
AI-powered packaging inspection methods help plants achieve sustainability and reduce waste by ensuring precise and consistent defect detection, which minimizes the production of defective products. Automated systems reduce the need for rework and the associated material waste, Kardam said.
“Additionally, by identifying defects early in the production process, AI helps optimize resource use and reduce the overall environmental footprint of manufacturing operations. Enhanced efficiency and reduced waste contribute to more sustainable and cost-effective production practices. Users can also see defect trends, which helps in identifying recurring issues and implementing long-term solutions to reduce waste. This methodology is beneficial for both package manufacturing companies and buyers of packages, such as FMCG, pharmaceutical, and logistics companies,” he concluded.
This article is from the February issue of Packaging South Asia