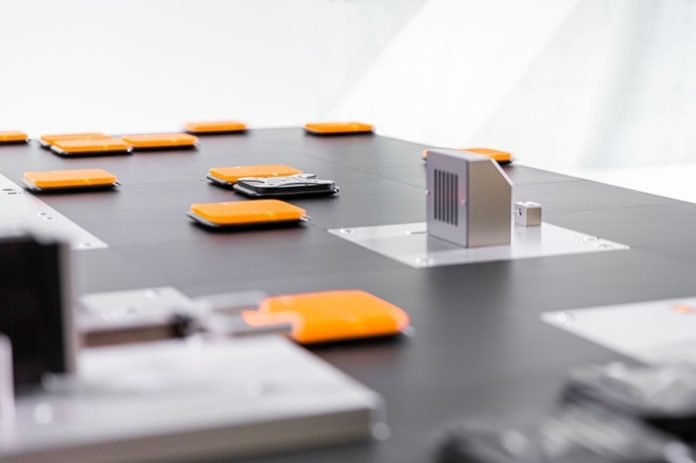
Consumer awareness is growing tremendously every day – influencing consumer purchasing behavior and pushing the packaging industry toward innovation. The final packaged product should be eye-catching with authentic details before reaching the market and, thus, is the last step of product packaging. With branding as the market catalyst, manufacturers want to attract with unique designs, shapes, sturdy packaging, and color pallets. Although end-of-line packaging may appear to be the least stringent component of any packaging unit, it is the most crucial because it will be placed directly in the hands of the customer.
End-of-line packing equipment is the last stage in the packaging process before the items move on in the supply chain. This is the primary reason why every packaging company requires a reliable end-of-line packaging solution for product shipping. Product protection during transit is ensured by automated systems such as palletizers, stretch wrappers, and case packers, which protect the product’s primary packaging during transportation. A product that is not properly wrapped or packed may have broken packaging. It will lose its marketability and needs to be thrown away since it is useless. This results in delayed product delivery to customers and damage to the company’s brand identification. Given the current shift in customer expectations and understanding, end-of-line packaging, the final and most crucial step of packaging, has become increasingly relevant.
The era of sustainable packaging
To be flexible, adjustable, and adaptable until end-of-line, manufacturers are responding to consumer demands while following current market trends. This allows them to work effectively together and adjust to packaging trends, which are a crucial component of the new era of sustainability requirements. Sustainability is a positive trend sweeping the packaging sector to reduce material and energy use. For this reason, tertiary packaging is a big investment for all manufacturers. Manufacturers are looking into every option to reduce waste and decrease excessive energy use. Manufacturers are assessing each acquisition component needed for manufacturing plants to reduce waste, use less energy, and comprehend the trade-offs between recyclable materials and carbon footprint. According to recent statistics, at least 25% of the biggest publicly traded firms worldwide have committed to achieving net zero by 2030. Sustainable manufacturing encompasses several global objectives such as cost, energy consumption, waste management, environmental effects, and worker safety and health.
ACOPOS 6D enables adaptive manufacturing
The packaging industry’s expectations in terms of technology have increased due to innovations. This has made it easier for packaging makers to connect with the consumer market by utilizing current technologies. Only with technological improvement will all of this be possible for experimentation, and unlike age-old techniques, the process will not be exceedingly long. Producers are willing to try and invest in new technical breakthroughs – the time needed to adjust to these developments is the only factor influencing their choices. As an innovation partner of OEMs and EUs worldwide, B&R has brought some of the best automation solutions to the table, giving them a competitive advantage. B&R provides end-of-line solutions as well as primary and secondary packaging solutions for all varieties of packaging machinery. The priority has always been meeting the specific needs of customers and assisting them in setting new benchmarks for adaptable, effective, and efficient packaging technology. With packaging being one of the important markets, end-of-line packaging is gaining a lot of importance today vis-a-vis sustainability issues. Adaptive manufacturing provides unprecedented flexibility. These machines enable users to master the challenges of product proliferation, mass customization, demand fluctuation, and shorter product lifecycles. Flexibility fuels adaptability, which makes short runs as efficient as conventional high-volume production.
B&R has always assisted the manufacturers in experimenting and achieving the necessary performance through a recent invention based on magnetic levitation, in which B&R’s ACOPOS 6D allows items to move freely across an open production area, thereby expanding the packaging’s potential for flexibility. As each product makes its way through the system, it can be tilted, rotated, raised, lowered, and weighed. The system allows for mass customization on the manufacturing floor, minimal footprint, profitable small-batch production, and instantaneous changeover on the fly. The ACOPOS 6D removes all wear, friction, and contamination – it is perfect for handling goods in cleanrooms and other carefully regulated settings found in the food and pharmaceutical industries. Thus, your end-of-line packaging can surely be adaptive by just inculcating ACOPOS 6D with your existing packaging facility. ACOPOS 6D has a sustainable future and will help manufacturers achieve more with this planar product transport system that makes it easier to set up processing stations and allows more output from a smaller footprint.