
In our previous issue, we wrote about our visit to Toppan Speciality Films’ Chandigarh office and our interaction with Manohara Kumar, CEO, and Whole-Time Director, who spoke about the company’s plans, the launch of GL films in India and the need to find sustainable alternatives. The insightful meeting followed a visit to Toppan’s plant near Ropar, away from the hustle and bustle of city life.
The drive from Toppan’s Chandigarh Industrial & Business Park office to the Bhai Mohan Singh Nagar plant through the state highways took about an hour. As you take a left from Rupnagar to hit the Ropar-Balachur road, you can almost hear the silence of the countryside with the density of speeding vehicles coming down. A few minutes after crossing the Sutlej, we could see the sprawling Toppan Speciality Films complex – flanked by the Sun Pharma and Centrient Pharma factories on one side and an offshoot of the lower Shivalik hills on the other.
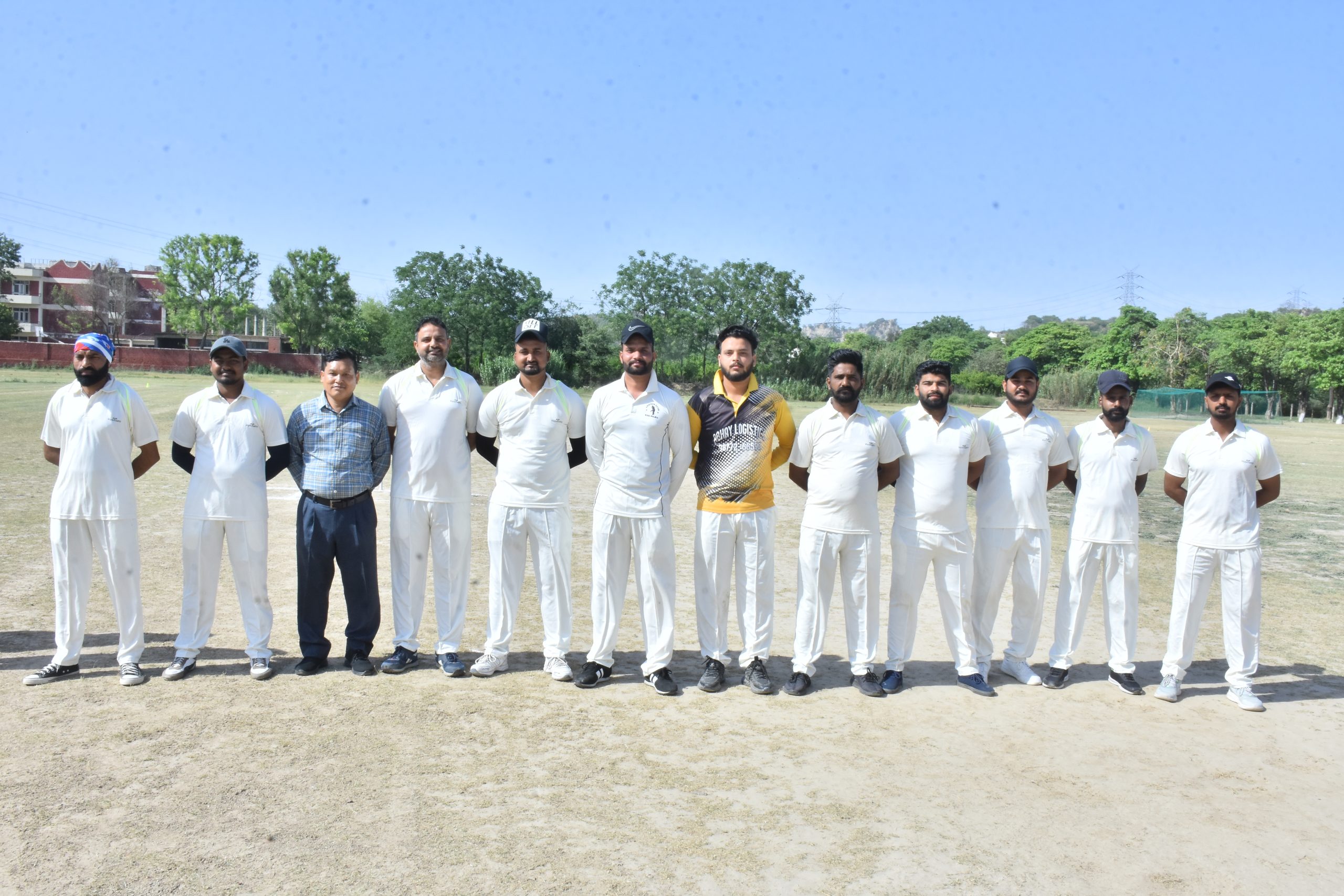
As I entered the clean and well-laid-out premises with manicured lawns, it was just past lunchtime. A group of employees were playing a game of cricket in the playground. An employee escorted us to Kirat Brar, the Head of HR & Admin, and our point of contact. After a brief introduction, it was time to see the plant. With safety boots, a head cap, and a factory jacket, we set out to watch the Toppan Speciality Films’ star attraction in action – the 5-layer BOPP (biaxially oriented polypropylene) line 5. I was accompanied by Kirat Brar and Head of Operations – Navneet Malhotra, one of the senior most employees, who knows the plant like the back of his hand.
Needless to say, the giant Bruckner BOPP line housed in an equally colossal shed was quite impressive, stretching for more than 100 meters. Malhotra explained how the hot melt passes through a die before it solidifies and then through extruders for biaxial stretching to the desired thickness for strength and flexibility. The BOPP line 5 has as many as five extruders.
The machines run 24/7 with a monthly downtime for regular maintenance and a yearly shutdown for an overhaul. Most of the work is automated with human intervention at crucial places for monitoring and quality checks. A control panel in the central monitoring room helps keep an eye on the entire process and ensures smooth operations. Safety is of paramount importance here as we were vacuum-cleaned in an entry chamber to remove any dust before we could step into the operations area.
As we have already written in the previous issue, a new hybrid BOPP-BOPE line is set to become operational by mid-2025, for which work is going on in an adjacent piece of land in full swing. The new and bigger line, which adds to the four working BOPP lines, will help the company augment its present capacity of around 80,000 tons per annum (TPA) and meet the increasing market demand.
Just as we exited the BOPP unit, two gigantic towers caught my attention. As Malhotra explained, these are material storage silos that are used to store raw material (PP granules) or reprocessed granules, which are created by recycling damaged or discarded films. These are then used during the film-making process all over again.

The next stops were the coating and metalizing units – processes that give the much-needed barrier properties to its flagship transparent high-barrier barrier film – and a glimpse of some slitter units. An employee explained how the coating and metalizing process works. Keeping the sustainability part in mind, there is an increasing trend among speciality film producers such as TSF to replace non-recyclable multi-layer packaging structures with mono-layer coated substrates that have high barrier properties.
Earlier known as Max Speciality Films before it was acquired by the Toppan Group, TSF has continued to strengthen its position as a leading supplier of speciality packaging, including sustainable ultrahigh-barrier solutions, and value-added products for labels, coating, and thermal lamination films for the Indian and overseas markets. It works with converters such as UFlex, Amcor, and Huhtamaki, and its clients include Pepsi, Unilever, Perfetti, Nestle, Marico and ITC among others.
The factory has six vacuum metallizers, three thermal extrusion laminators, three coating lines, and one CPP line. TSF, which has more than 20 slitters, including primary & secondary slitters, has also ventured into the production of masterbatches.
The cast film line (CPP) unit was the next stop. The impressive W&H Filmex II line comes with five extruders mounted on the top. Like the BOPP line, this unit too had a recycling unit to minimize wastage. A new 7-layer CPP line along with three more metallizers will soon be added to its arsenal. We also saw how the final products are cut as per requirements and packed and loaded onto the waiting trucks for their final destination.

As the CEO had earlier explained, the first BOPP line was operationalized in 1990 when the company was still Max Speciality Films followed by the first metallizer in 1996. In 1998, coating lines were introduced. In the year 2001, the first thermal line and the second BOPP line came up, and then in 2003 and 2006, the second and third metallizer units. The fourth BOPP line was introduced in 2011 and line 5 in the year 2015.
The company, which has won multiple awards, including the India Star and World Star awards for product innovation and the coveted Golden Peacock Award for quality and safety, houses more than 500 employees on rolls apart from other workers, Brar explained. The majority of the employees are from nearby villages, which helped the factory function even during the Covid lockdowns, barring a brief lull.
The campus, which is spread over 30 acres, has a 132-KV power plant for uninterrupted supply. A fraction of the power needs is met by solar energy.
After a brief conversation with Brar and Malhotra in the conference room, it was time to bid adieu. The game of cricket was over by that time and the employees were back at their workplace. I boarded the car back to Delhi with an educative experience and some rich insights.