
Earlier this week I wrote about the three new inkjet presses that Canon is developing, including two that spearhead a new move into the packaging market. All of these presses are underpinned by a common imaging platform based on a new printhead that Canon has been quietly building towards over many years.
Up to now, Canon’s inkjet production presses have mostly relied on Kyocera’s bulk piezo printheads. That’s hardly surprising, since Canon’s first inkjet press was the Jetpress, which was built by Miyakoshi in Japan, and Miyakoshi has generally favoured Kyocera heads. Canon continued this trend, even as it took over the development of more and more of the sub-assemblies that make up these presses.
But in the background the European operation, Canon Production Printing, or CPP, which grew out of Canon’s acquisition of Océ, has been developing its own piezo printhead designs. At first these were used with some of Canon’s wide format printers, starting with the ColorWave but more recently also including the Colorado series.
Canon has always been very reluctant to talk about the development of its piezo printheads but the announcement of the new presses has forced the company to be a little more forthcoming. Thus Canon has confirmed that it has designed and built a completely new piezo printhead. This head is designed by CPP in Europe, and is built by Canon, but the company won’t yet say where, other than that Canon owns the manufacturing plant. Roland Stasiczek, senior director business development for packaging at CPP, says, “This means that we have complete control because they are our own.”
The new printhead is a thin film Silicon MEMs piezo head, which means that Canon has made a significant investment since anything that involves Silicon MEMs is expensive. The advantage of using the MicroElectrical Mechanical systems or MEMs approach, which is essentially semiconductor technology, is that it allows a lot of very precise control to be built into the printhead while still achieving a very compact form. A further advantage is that it’s hard for other head manufacturers to compete because of the eye-watering level of investment needed to build a suitable manufacturing plant, as Xaar discovered to its cost when it had to abandon its own thin film ambitions.
Canon is using the established sol-gel process in which a material starts off as a colloidal or mixed solution that is then formed into a gel-like substance. This is widely used with a number of different materials, including ceramics and silicon. It can also be used with lead zirconate titanate, better known as PZT, the piezo-electric material that forms the basis of many inkjet actuators. The typical approach for building a MEMs actuator is to create the PZT through the sol-gel method and apply it through spin coating as a thin film on top of a silicon wafer. This same approach is also used by Ricoh for its MEMs printheads.
Although the design has come from CPP in Europe, the level of investment suggests a deep involvement from Canon Inc in Japan. It’s also worth noting that Canon has a separate division that makes a range of equipment used to produce semiconductors and is highly experienced in producing industrial electronics.
Canon has no plans to sell its printhead to other vendors, at least for now. Instead it is planning to use the same printhead and imaging system across a range of presses, effectively giving it a common platform that includes the heads, primer and inks. Stasiczek explains, “The platform approach means that these heads are used in all our products and that’s how we get the volume to get the return.”
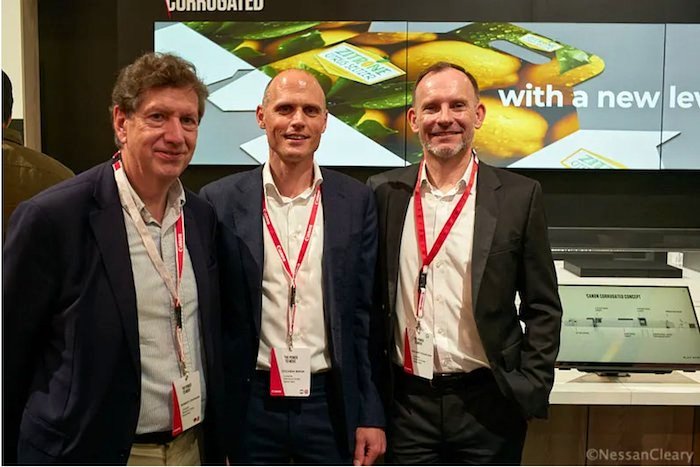
As yet, there is no official name for this new head, and very little detail in terms of specifications. The new printhead is designed for single pass applications. It’s a greyscale head and can produce 1200 dpi resolution. It runs at 40-70khz, with a native drop size of 2-3pl. It can handle water-based fluids with a viscosity of 2-6 milliPascals.
I’ve been told that Canon spent a lot of time ensuring the optimum width to allow it to use the same printhead in printbars of various lengths for different presses and formats before settling on a print swathe of roughly 100mm.
The head features recirculation and also includes compensation for blocked nozzles, based mainly on printing larger drops either side of the missing nozzle. Stasiczek explains, “It has an acoustic feedback so we know what’s happening in the heads.”
see also
Canon’s move
into packaging
The heads have a parallelogram shape, similar to the Fujifilm Samba heads, for the same reason – to allow the heads to be slotted together in a series along a printbar. Ronald Adams, vice president of sheetfed presses for CPP, explains, “We want to have the print unit as compact as possible because only after that can we start drying and we want to start drying as soon as possible. And we don’t want a long time between the first color hitting the paper and the last color.”
Nonetheless, I think it’s fair to assume that Canon is hoping to compete directly against the Fujifilm Samba head in terms of features and capability. Both the iV7 platform and the Corrugated Concept press will use this new MEMs piezo printhead. The B2 VarioPress uses eight printheads per color while the B1 corrugated press has 18 heads per color.
Thermal ink technology
In addition to this new thin film piezo printhead, Canon has also taken its thermal printhead technology, which is widely used in office and large format photoprinters, and developed a new thermal head series for commercial print use. This has led to two further presses. The VarioPrint iX1700 is a sheetfed press for commercial printers, while the LabelStream LS2000 is a label press, both of which I’ve previously written about here. They were shown off first in Yokohama in Japan at the end of last year, before making their European debut at Drupa this summer.
In both cases, there is a single printhead per color with the print swathe of the head matching the print width for the press. Both presses use the same type of head, with the only difference being the print swathe, which is 340mm for the LS2000 and 360mm for the iX1700. This means that there is no need to stitch multiple heads together, and there is no need to calibrate or align heads as is common when replacing one head in a printbar, making head replacement relatively straightforward.
However this also means that there are a lot of nozzles on each head and it only takes a handful of these to fail for the entire print bar to have to be replaced. Canon says that these thermal heads use ink circulation technology that helps keep the ink moving along a precise flow path to the tips of all the nozzles, which should ensure optimal ink consistency and jetting behaviour. In addition, Edoardo Cotichini, senior manager for label and packaging for Canon Europe, points out that Canon has developed some cleaning routines that involves spraying a cleaning liquid and then using a roller to clean the heads and hopefully clear any blocked nozzles.
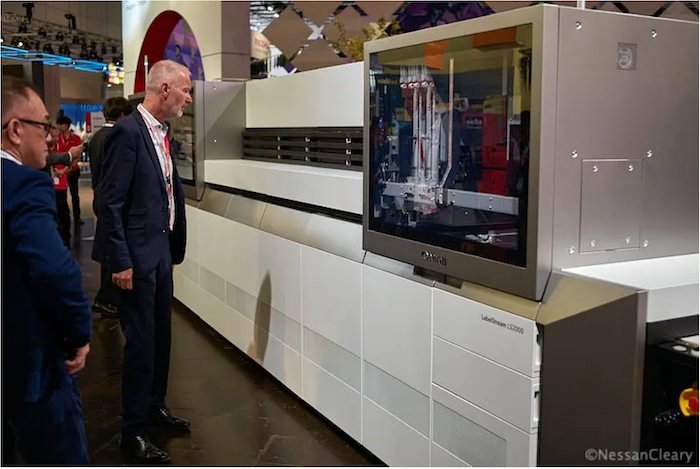
Canon is not yet able to talk about the expected lifetime of its thermal heads though this will obviously have a major impact on their value proposition. Thermal heads are generally regarded as a consumable item, but HP and Memjet have both demonstrated that it is possible to get a reasonable amount of use from this head technology, and the ink recirculation and cleaning methods that Canon has implemented will go a long way to help with this.
Water-based inks
All of these new presses – the VarioPress iV7 and its folding carton variant plus the corrugated concept press that I covered in the first part of this story, which use the new piezo printhead, as well as the VarioPrint iX1700 and LabelStream LS2000 that use the thermal printheads – use a similar water-based ink, albeit with different formulations according to the head technology and substrate. This is the same resin ink technology that Canon developed for its existing inkjet presses, including the ProStream series.
The ink itself is a water-based polymer pigment ink that contains resin particles with highly saturated pigments. Resin inks depend on heat to melt the resin and bond the pigment to the substrate. In this case the pigment-to-resin ratio has been optimised to form a very thin ink film after jetting, which suppresses the internal scattering of light, allowing a wide colour gamut to be reproduced. Stasiczek notes, “There are co-solvents in the ink for the jettability to keep the nozzle open.”
The first printbar within the presses is used to jet the primer, which Canon calls ColorGrip. The primer drops are placed in exactly the right place to catch the ink drops which follow. Once the ink is jetted the ink drops are first pinned to stop them from moving around, then subjected to heat to cure them and humidity to complete the fixation. Once the droplet hits the substrate surface the water content is evaporated or goes into the media.
The ink formulation also helps to reduce the amount of drying power that’s needed. As long as the particles are contained within liquid, they repel each other, which helps to maintain the dispersion of those particles. Stasiczek explains, “Once the ink jets to the paper and the water goes out then the particles start to agglomerate and they push out the remaining liquid. And then we get an even flow. And this is the same principle as the iX-series and the ProStream. We are not evaporating any co-solvents; they go into the paper, so they are included in the indirect food contact label testing. We make sure the ink ingredients are as safe as possible. Every component has specific regulatory levels.
Robert Crooker, senior director strategic portfolio management, adds, “The problem is that the regulation changes and that’s the biggest challenge.” He says that it’s a balance between productivity and quality and cost. Nonetheless, the ink will be certified for indirect food contact, which many converters regard as essential for all packaging and labelling applications.
Labels and packaging
Canon has long harboured ambitions for the packaging market, going all the way back to the Océ InfiniStream, which was developed as a B1 press for folding carton. It was based on liquid toner technology and was installed at a German beta site in 2013 but finally abandoned in 2016.
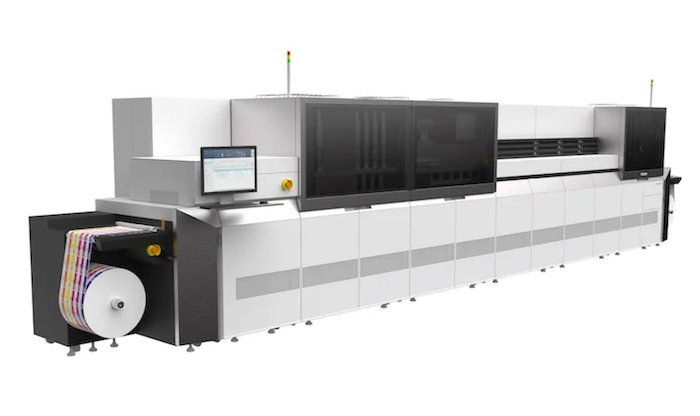
Canon has had a slightly haphazard approach to the digital label market, starting off with the LS4000 press. This was heavily based on the existing FFEI Graphium, which had already been around for a while but allowed Canon to get to market quickly without having to develop a new machine from scratch. Then Canon surprised everyone last year by acquiring the British flexo press manufacturer Edale, which had provided the chassis for the Graphium. But the logic seems to be that Edale gives Canon a way into the established label printing market, and increasingly also the folding carton market, through Edale’s installed base of narrow web flexo presses.
What is clear is that despite its late market entry, Canon now has a multi-pronged strategy for addressing the labels and packaging sectors, starting with entry level labels and up to B1 folding carton and corrugated machines. Moreover these presses are already tightly integrated with the rest of Canon’s print portfolio, including both its wide format printers and commercial presses. Most importantly, Canon owns the IP behind the inks, the press chassis and transport systems and of course the new printheads.
Canon is now in the unique position of having two viable inkjet technologies for the commercial and packaging print markets. The development behind the new MEMs piezo head appears to have been led from CPP in Europe, while the thermal printheads have clearly come from Canon Inc in Japan. That said, Canon’s staff were at pains to point out that there has been close cooperation between the two Canon’s – CPP and Inc – for both the printheads and the presses.
For now, the two presses using the thermal printheads both appear to be aimed at the entry-level, or at least the more price conscious, market. However, it is expensive to develop inkjet technologies, so it remains to be seen if Canon feels that it’s worth the R&D cost of advancing both its piezo and thermal printheads. Part of that calculation will depend on whether or not Canon wants to offer these heads to other OEMs, as other Japanese press manufacturers such as Ricoh and Epson already do with their printheads. In any case, it’s going to be interesting watching how Canon develops its inkjet technology and presses over the next couple of years.
You can find the first part of this story – Canon’s move into packaging – here, and more information on Canon’s production printing offering from global.canon.
First published by the Printing and Manufacturing Journal on 17th September 2024. Reprinted by permission. www.nessancleary.co.uk