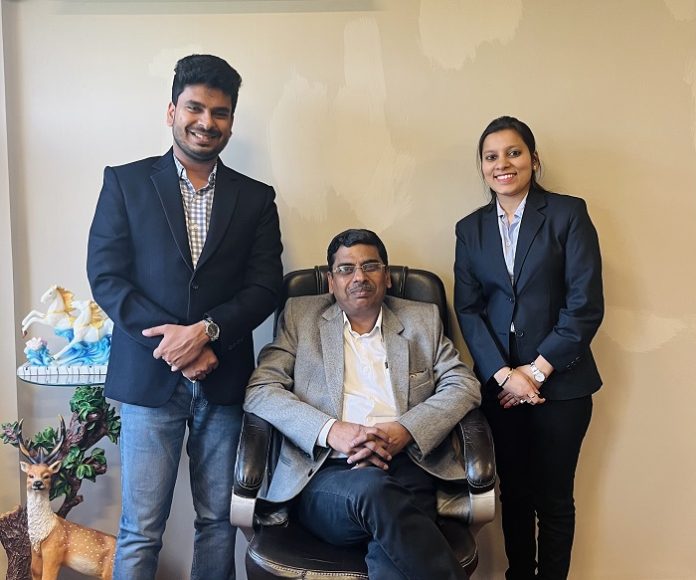
Omega Printopack is a first-generation packaging company in the Sidcul industrial area of Haridwar in Uttarakhand. It’s run by founder and chairman Sandeep Kumar Jain, his son managing director Akshat Jain, and his wife Manushtha Jain who looks after HR and finance.
The business started in Delhi’s Jhilmil industrial area in 2003. It was then relocated to Haridwar in 2010 to take advantage of the generous benefits and excise duty reductions provided to businesses in Sidcul by the Uttarakhand government. Benefits accrued from the sprawling and geographically well-located industrial area include lower electricity costs and other amenities. The area was less polluted and proximate to consumer product clients and larger areas suited the company’s plans to enter the corrugation segment. To be near its new plants, the owners relocated to Ranipur in Haridwar.
Omega Printopack’s four plants in Sidcul, Haridwar manufacture monocartons in locations 1 and 3, while corrugated cartons are produced in plants 2 and 4. These comprise 70,000 square area of built-up space The four packaging plants are spread across 70,000 square feet. There is a fifth space of 35,000 square feet for warehousing. The company’s combined production is approximately 11 lakh (1.1 million) cartons daily adding up to 3 million each month.

The four plants serve mostly Rudrapur, Roorkee, Selaqui, and Dehradun in Uttarakhand with a 98% share. The remaining 2% goes to the Delhi-NCR, Uttar Pradesh, and Baddi in Himachal Pradesh. The company plans to increase its share of FMCG customers currently at 3 to 4%, while pharma customers make up a 50% share and electrical goods contribute 40%. Cosmetics make up about 3% with another 3% coming from miscellaneous sectors.
Plant 1 – short-run monocarton jobs
Plant 1, launched in 2010, produces small lots of 5 to 10,000 monocartrons and inserts. It houses the Omega Printopack group headquarters and a production area of 20,000 square feet. Running at full capacity of 4.5 to 5 lakh cartons and 1 to 1.5 lakh inserts daily, the plan is to increase capacity by merging it with an adjoining 50,000 square foot space.
Plant 1 is equipped with a Komori Lithrone S32 4-color offset press and a Heidelberg single-color perfector for inserts. Three Pratham folders can provide 4-, 6- and 8-fold for pharma inserts inline.
Ancillary finishing and converting equipment include an AutoPrint UV coater, three manual die-cutting machines, and a Bobst Novacut 2.0 (2017 model) autoplaten die-cutter. A Bobst Ambition 2015 model folder-gluer, an Acme side-pasting machine (2010-11 model), and an Autoprint Checkmate quality inspection of cartons round out the converting section. The expansion plans envision the addition of two Komori 4-color 40-inch presses, a pair of Alpana coaters, and a lock-bottom pasting machine.
Plant 2 – 3-ply printed corrugated cartons
Plant 2, started in 2018, prints 15 tons of 3-ply printed cartons per day in its 15,000 square feet. At 60% capacity, the plant currently manufactures one lakh corrugated cartons daily. Two corrugators from Micro – a 42-inch e-flute, and a 52-inch a and b-flute corrugator, and a high-speed e-flute corrugator from Ample Graphics produce the corrugated boards.
The plant also has one laminator for sheet pasting from Taiwanese Paktek along with four Indian die-cutting machines and one auto die-cutting machines from DGM. There is a DGM Technofold for folding gluing. The company also has a DGM SmartFlute X 1450 automatic flute laminator in Plant 2.
Plant 3 – longer run monocartons
The third plant of Omega Printopack, began during the Covid-19 pandemic in 2020 to produce longer monocarton runs with quantities of 1 lakh and above. It is presently running at 50% of its daily 16-ton capacity or about 6 to 7 lakh monocartons daily.

This plant has two Komori G540 5-color plus coater presses, a Heidelberg CD 92 press, and an Alpna Rhinodexa for UV and texture coatings. A Bobst Novacut 3.0 (2023 model) die-cutter and a Bobst Expertfold (2023 model) folder-gluer round out the converting section. Omega Printopack has a Siegwerk ink kitchen in-house with two Kodak CtPs for prepress.

Plant 4 – mastercarton corrugation and conversion
The fourth plant, launched later in the Covid-19 pandemic during 2021 comprising a 15,000 square-foot area currently converts 15 tons of corrugated mastercartons daily. Presently operating at 60% capacity, 40,000 shipper cartons each day.
Together with two machines from Micro – a 42-inch corrugator and a 45-inch narrow flute corrugator, and a Sujata 52-inches narrow flute machine and an old Indian flexo printer, the plant has four local manual pasting machines and five locally manufactured manual die-cutting machines along with a RS4 combined rotary creaser-slotter machine. It has five Indian manual stitching machines and a Universal carton folding machine.
Akshat Jain, managing director of Omega Printopack, joined the company in 2018. He says Komori provides excellent 24×7 service and prompt feedback. Apart from its competitive prices, he says his good working relationship with its team including Jitendar Rohilla helps in decision-making for the future. According to him, the printing quality of the presses is very good.
In addition, Bobst and DGM machines provide precision and quality in the converting workflow, says Jain, adding that he generally gets useful inputs from Bobst’s Arvind Dhand and DGM’s Puneet Agarwal. Completing the testimonials to his suppliers, he adds, “Pratham provides economical machines for good quality inserts. Their drupa24 stand made a positive impact for Indian insert machines at the show in Dusseldorf this May-June.
According to Jain, packaging has a profound impact on brands in the market. After the Covid-19 pandemic, consumers no longer want to buy loose commodities and goods leading to a rise in packaging. “We aim to reduce dependency on plastic and focus on paper,” he explains, adding, “eCommerce has led to a definite shift in packaging as it acts as protection for the articles inside. The real challenge in that segment is how to protect while being visually appealing.”
Apart from competitive pricing, new brands want short-run jobs with smaller lead times. Earlier, short-run jobs would come with lead times of 8 to 10 days but nowadays, brands want instant results.
On the fluctuation in paper and paperboard prices in the past two years, Jain said, “Paper prices have fluctuated drastically in the past two years, reducing margins. We centralize our paper procurement in rolls from ITC, Century, Emami, Khanna, and JK Paper, which are then converted into sheets of appropriate sizes.”
According to Jain, Omega Printopack’s USP is its high-quality production without compromise, resulting in client satisfaction and repeat orders. Omega Printopack’s FY23-24 turnover of Rs 80-85 crore is expected to cross Rs140-crore in FY 25-26.
Expansion in capacity and diversification in market segments
In November 2024, the company will merge plants 2 and 4 into the new 1 lakh square foot building under construction. The new facility is expected to generate a corrugated carton capacity of 40 tons daily.
The goal-oriented Jain says, “We are continuously working toward our goal of being one of the top carton manufacturers in the country.” His diversification plans include pulp molding and packaging and aluminum foil blister packs for the pharma market. To capture a larger share of the FMCG market the company is working on its BRC and ISO certifications.
This article has been slightly modified by the author on 3 September 2024.