
Duesseldorf, Germany based system provider GEA announced in early June its Orbital Cleaner OC200 solution for the cleaning of hygienic process, storage, and fermentation tanks of all sizes. The modular solution is aimed at the food and beverage industry, as well as in the healthcare, chemical, marine, fish farming, bio-ethanol, and wine sectors. With its hygienic design and the use of FDA-compliant materials, the OC200 developed by GEA is suitable for use in the food and pharmaceutical industry.
It is also relevant in the paint and coatings industry. After its premiere at the BrauBeviale 2019 in Nuremberg, the official sales launch of the new modular orbital cleaner OC200 has now begun. It is available immediately.
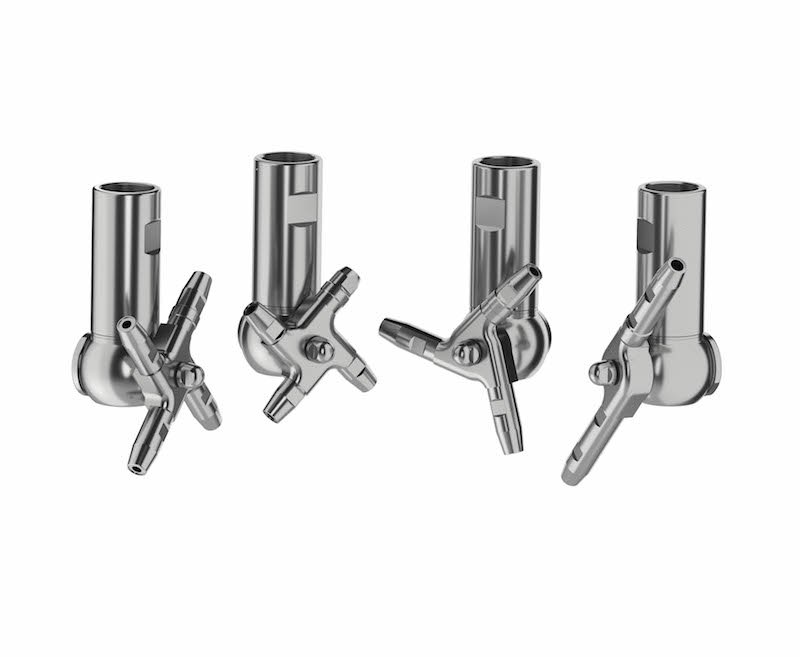
How an orbital cleaner works
Equipped with two, three, or four nozzles of different length and diameter, the OC200 rotates around the horizontal and vertical axis. The nozzles’ internal profiling creates a high impact jet, which ensures intensive cleaning of the inner surface of the tank or container at pressures ranging from 4 to 10 bar. A wide range of tank sizes up to a diameter of 36 meters can be cleaned with variations in the number of nozzles, variable nozzle diameters, lengths, and rotation speeds.
Modularity as a real customer advantage
The modular concept allows easy exchange of components, such as the rotors, nozzle carriers, and nozzles, in various standard versions, while the remaining components do not have to be disassembled. This modularity allows a flexible adaptation to the process and customer requirements regarding cleaning diameter, installation opening, jet dwell time, and cleaning intensity, thus allowing optimization of the cleaning process, with reduced consumption of cleaning media.
Service and quality
Compared to other orbital cleaners, the Orbital Cleaner OC200 offers significant advantages in terms of cleaning performance, efficiency, quality, and durability. Also, the maintenance intervals are significantly longer compared to other orbital cleaners, which ensures more extended plant availability. The relatively small number of components within the cleaner, as well as the availability of standard service kits through the extensive GEA network, enable fast and cost-effective service and thus smooth operation.
The customer saves cleaning costs
The GEA OC200 saves both time and valuable resources (chemicals, water, personnel costs) by optimally adapting the cleaner to the process conditions. With extended maintenance intervals, the total costs of operation (TCO) i.e., acquisition costs, energy consumption, maintenance, and repairs, are low compared to other orbital cleaners.
Orbital Cleaner OC 200 – powerful and flexible
The Orbital Cleaner OC200 also offers further advantages when changing parameters in the existing cleaning process. Due to the exchangeability of components, it can be easily adapted to the new requirements. Customers know what they get from the new OC200 – optimized cleaning performance that helps protect their end product and brand by preventing contamination and increasing process reliability.
Editor’s note: GEA is active in India with an office in Vadodara. It has been a major supplier to Amul for its modern integrated dairy plant expansion. The company is also active in the pharmaceutical, alcobev, and chemical space, all industries in India that are relatively fast-growing. The vaccine production and blood plasma segments are especially important in the current situation of the Covid-19 pandemic. The company is also a supplier of vertical form fill and seal machines for various food and confectionery products.
The company has more than 100 years of experience in the pharmaceutical, nutraceutical, biopharmaceutical, and biotechnology processes and manufacturing. GEA claims this expertise helps it to tackle the challenges and hurdles that enterprises face to achieve specific goals. Over time, GEA has established its name as a single-source supplier of process equipment for batch and continuous tablet production, contained materials handling, fermentation, separation, and lyophilization. It was a very visible and active exhibitor at the recent CPhI & Pmec event in Greater Noida in November 2019. We hope to write more in the future about GEA’s activities in India.