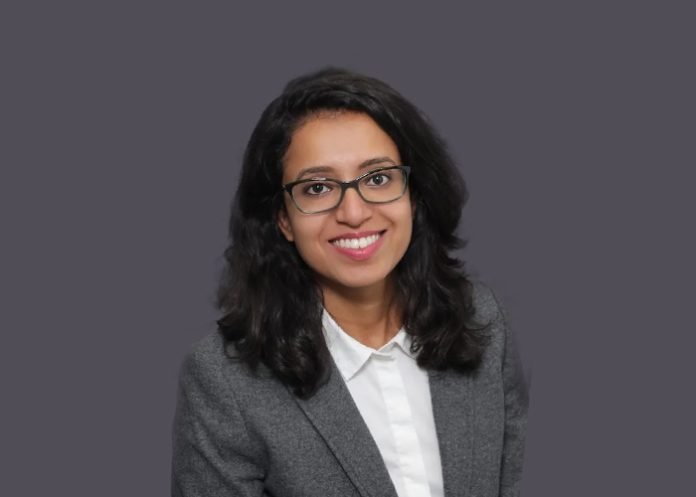
Dr. Dipshikha Banerjee, Siegwerk’s Head of Technology for flexible packaging for the India Region discusses some of the ink and coating developments the company is bringing to market for improvements in film and paper packaging, especially for food products.
Low migration inks for food packaging and inks with improved sustainability profile have been the key focus areas in Siegwerk’s inks and coatings for paper, cartons, labels, and flexible packaging using offset, gravure, and flexo printing. We used the opportunity of a web meeting with Dr Banerjee to ask about developments such as flexible packaging, moving to pauperization, and the increased interest in water-based inks for gravure and CI flexo presses for printing on films and laminates. The conversation veered to water-based inks and the printable coatings that the company is developing and bringing to market for adding functional and barrier properties for both paper and films, which can assist in making those materials more easily laterally recyclable.
Dr Banerjee broached the subject by saying that for paper bags, and corrugated materials water-based inks are widely used. “For any water-absorbing substrate, water-based inks are a natural and established choice. Paper cups and plates often have plastic coating to protect the food and beverages served on them. We now have developed functional barrier coatings that can replace that plastic so that the paper plates and cups can be plastic-free and fully recyclable.”
see also
Siegwerk talks about
water-based inks for
flexo printing at
Speciality Films
summit
On the trend or aspiration to use more paper instead of flexible films for packaging food products, Dr Banerjee said, “When we move from today’s plastic material-based structure to a paper-based structure how do we compensate for the barrier properties those structures are providing today? Same holds true for transitioning from a multi-material laminate to a mono-material laminate. Barrier functionalities such as moisture vapor barrier, oxygen barrier, grease barrier are essential for us to transition. For these reasons, we are working on developing functional and barrier coatings suitable for both plastic films and paper-based structures. To extend paperization further, we additionally require a heat-sealable lacquer that can replace the sealant polyolefin and is appropriate for direct food contact. This is something that we are developing further.”
We ask, “Do you think that paperization will come to India also beyond the odd organic protein bar? Some industry insiders say that it is merely a greenwash and there is the higher price of fiber-based materials in comparison to the price of polymers to consider in a price-sensitive market?” Banerjee affirms that it will happen, “It will. Brand owners are looking to replace some multi-layer multi-material flexible packaging with mono-material structures or paper materials. So, brands are seriously exploring paperization as an alternative.
“However, there have to be regulations to push brands in this direction – regulation plays a big role in industry movement. The brands will start slowly with one or two products. In Europe, Hershey and Nestle already have paper-based packaging for their chocolates and it is likely they will also introduce them to India.”
Banerjee further explained the role that coatings can play in sustainable flexible packaging, saying, “Barrier properties can be built into a film that is recyclable, but if you have a printable coating with barrier functionalities, you have much more flexibility. You can simply print the coating on a film using a traditional printing method like flexo or gravure. Some of our printable barrier coatings are already commercialized. They are available in India and we are conducting trials with customers and are in the process of rolling them out.”
Functional barrier coatings are essential for mono-material structures. She mentions another functional coating called Heat Guard, developed by Siegwerk for increasing the heat resistance of PE films that are often seen as a suitable mono-material alternative to mixed plastic laminates. “Unlike polyester which is robust, PE films have less heat resistance and if you are using MDO PE, the Heat Guard coating can protect the structure to withstand and survive the post-printing and converting processes.”
She adds that an oxygen barrier coating can be applied on the base layer of a laminate by applying the coating on a unit of a gravure press or a CI flexo press. A transition from a reverse printing structure to a surface printed one with suitable functional barrier coatings is another approach that paves the path towards sustainability.
Commercializing water-based ink systems for flexible packaging in India
Currently there is a great deal of interest in using water-based inks for flexible packaging using both the gravure and flexo process. Siegwerk is active in this area and Banerjee explains that firstly, there is a technological challenge beyond the oven capabilities needed to cure water-based inks – maintaining the barrier properties and the strong adhesion for lamination.
“The second problem is the thought process,” she says, adding, “Technically we now have solutions for water-based inks for non-absorbent materials, but we need presses that have the requisite oven temperature and good evacuation of moisture. You need to have that airflow to decrease the humidity in the oven. Foaming is also a problem but can be tackled in several ways – on the machine side or in the ink formulation.”
We ask if water-based inks are more food product friendly, sustainable or have a better carbon footprint than printing with solvent-based inks on flexible materials. “There is no inherent advantage in food compliance or less migration,” she says, “And, both processes are equal in carbon footprint. But you are removing the VOC content in water-based inks so that is inherently safer for the pressroom personnel and also reduces the danger of fires and explosions. Solvent-based systems may have some ink trapped or traces. But, with the right systems and processes in place, both solvent-based and water-based inks are effective and safe for food-related flexible packaging.”
Water-based ink systems offer many advantages over solvent-based inks, including lower effluents, lower fire hazards, improved occupational safety, excellent printability, suitability for food applications, printability at high speeds, and easier viscosity control. Banerjee stated at the Elite conference in Mumbai last year that Siegwerk is very confident about the two types of ink systems, for surface as well as reverse printing. According to her, the cost of water-based ink systems is almost at par with solvent-based ink systems.
Siegwerk continues to conduct trials and commercialize its water-based ink systems in the Indian market. Banerjee notes, “Technically these two systems are ready and Siegwerk is now looking for partners to commercialize these solutions in the Indian market. We see huge potential for these inks as both brand owners and end consumers are now extremely receptive to such eco-friendly solutions when it comes to flexible packaging. Some policy support from the government will also help in making such environmentally friendly ink systems more popular.”